Universal cargo platform 0.5
Let's consider in more detail already in relation to practical implementation. To do this, we will use a small-sized project of a Universal cargo platform 0.5.
I'll start the device with the control system. The control system is based on an Arduino controller. This is very convenient when designing, when you don't know what you might need. I am using an Arduino Mega 2650 with a shield for a 3d printer RAMS 1.4. This bundle allows you to connect 5 stepper motors at once. If you need more, this is not a problem as there are a lot of free pins. It is possible to use UNO with a 3-ver CNC shield. 4. There are 4 drivers available, but very few outputs.
Stepper motors will be used as the main drive. They have a large starting power and the exact number of revolutions that can be set. Therefore, it is enough to have one end cap to fix the initial position. After that, you can ask to make the required number of turns and if there are no obstacles, then he will do them. To work with a stepper motor, you need a driver who will control it. The drivers must be used according to their power. You can also put additional current sensors to understand when the engine is running with a large cut and turn it off in time so as not to lead the structure to destruction.
End caps. To work successfully and understand the position of the mechanism. In order to have full control over the mechanism, the end caps must be used at each key point of its movement. But it's not very convenient. The use of a stepper motor allows the use of a minimum of end caps. But we must remember that if the load is excessive, the stepper motor will start to slip (knock). The end caps can be both mechanical (contact) and non-contact. It is preferable to use contacts without them, but it is not always possible.
The station controller is controlled by means of codes. The connection is made via the serial port at a speed that is set by the firmware of the controller. You can connect to the parallel port either to a computer or an Arduino with wifi for wireless access. Management takes place using code commands. The list of commands available to the user is given here. The controller also reports on its status of command execution and possible errors. These messages can also be stored in additional programs that work with the station.
Demonstration of the model's operation. Vox is used for frame 250.
This video clearly shows how the mechanism of the cargo station works. The main mechanisms are a carousel rotating around its axis and a lift moving up to the bottom. The carousel provides the supply and clogging of cargo from the lift. The lift provides reception and loading of cargo and battery from the drone.
It all works as follows. A drone arrives. He sits down on the platform. After the positioning mechanism, the drone is installed above the reception window and fixed on the site. Simultaneously with the fixation on the site, the cargo acceptance window opens. After that, the lift rises under the load to receive the cargo. The cargo lock in the cargo container is lowered on the drone and the cargo is placed on the paw of the lift. After that, the lift descends and puts the load on the petal of the carousel. The carousel turns and a petal free of cargo stops above the lift to fit the battery. After that, the lift rises up and takes the drone's battery for replacement and lowers it onto the velcro. The carousel turns again and this time there is a charged battery on it. The lifter lifts this battery into the drone where it is fixed in the battery compartment by the battery clamps. After lowering the lift, the carousel turns again and the cargo necessary for transportation will already be located above the lift. After that, the cargo is lifted and fixed in the drone in the cargo department. After that, the lift descends to its fixed place at the very bottom. Next, the drone locking system switches to the closed position, freeing the drone and closing the shutters of the grog window. The drone is ready to perform a flight mission. The station starts charging the battery on the petal and is ready to give the accepted cargo through the delivery window.
This is a complete description of the operation of the station. Various other options are possible. For example, without replacing the battery if there is enough charge, or replacing one battery with a load or not.
For convenience, first consider the frame design of the universal cargo station (UGC). The frame for this model is made of 8 mm studs connected by inserts. The inserts are quite versatile and can be used in various combinations.
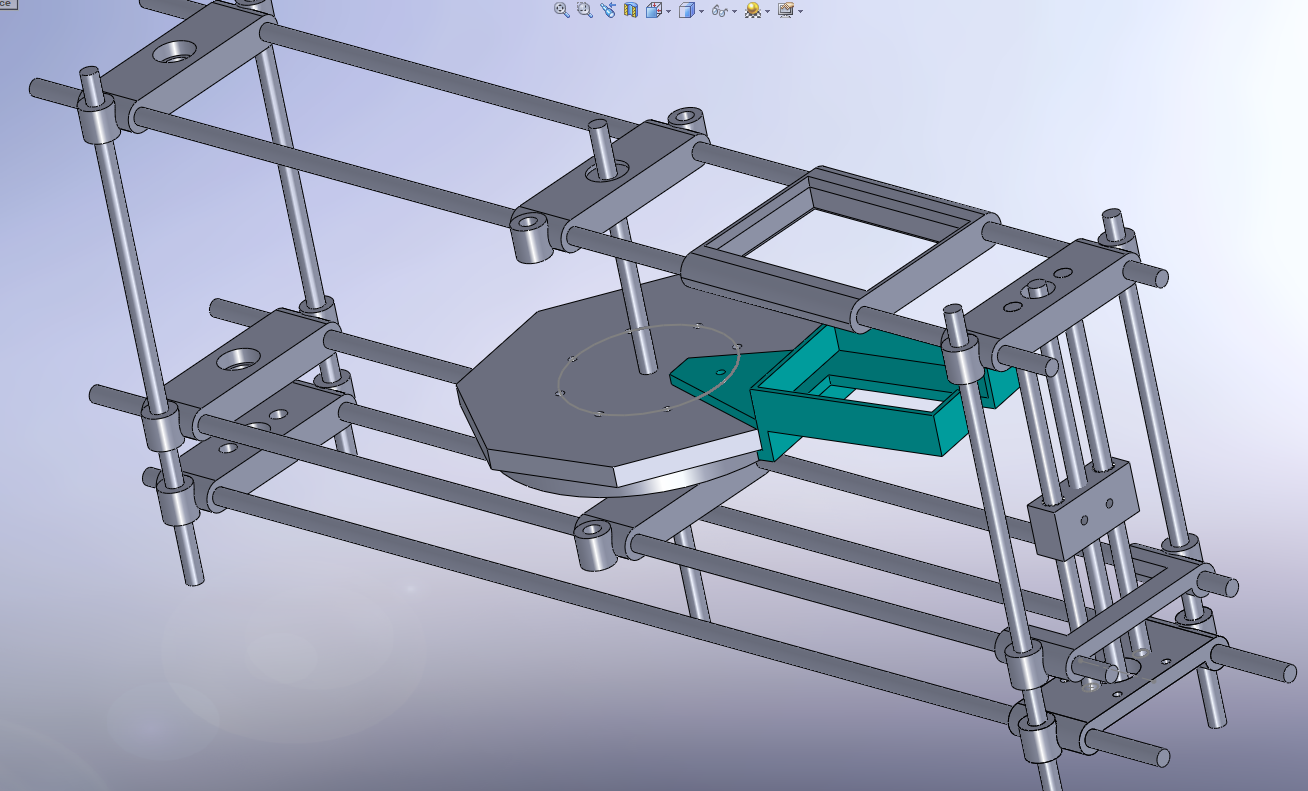
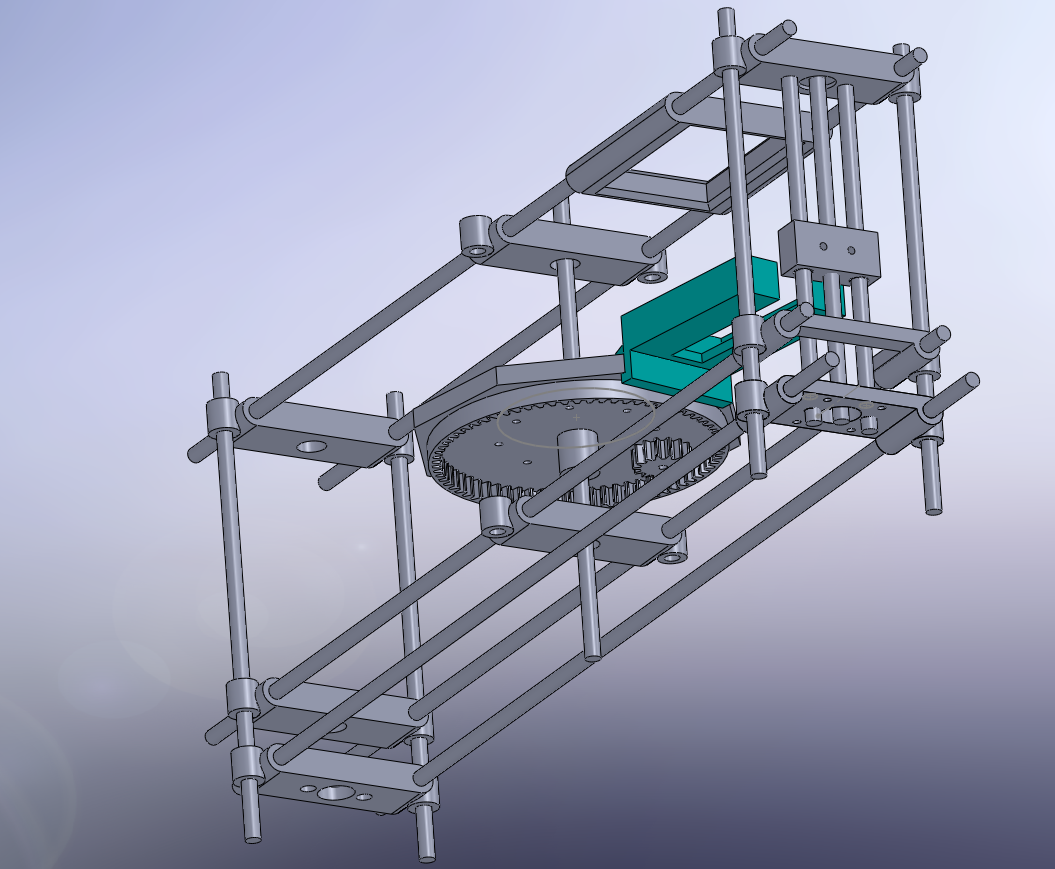
For convenience in understanding the design, the frame is shown without some important parts in the form of their stepper motor drives, end caps, lift legs, loading and unloading system, landing pad with positioning and locking system. But the lift carriage and the carousel drive gear are perfectly visible.You can also see that there is only one cargo petal, and not quite the final shape. A window is also visible for the correct cargo center for the delivery and reception of cargo from the flight deck.
Station commands.